Minor workplace incidents can mean danger is ahead
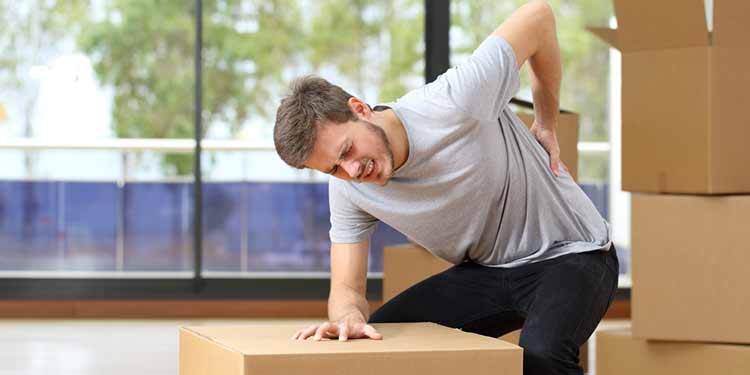
When workplace injuries are discussed or publicized, it is the serious ones that are front-and-center. They are the ones that cause the most pain in terms of injuries, cost, missed work time, employee morale, lost productivity, and more. If only, we could predict what incidents are on the horizon.
In a recent Institute of WorkComp Professionals (IWCP) teleclass, OSHA Record Keeping The Ultimate Predictor of WorkComp Performance, Dustin Boss, a Certified Risk Architect with Ottawa Kent Insurance, explained all businesses have solid, but often overlooked, data that can help predict what is going to happen. This is the data in the OSHA logs and Work Comp forms that give a complete picture of the injuries that have occurred.
Historical studies document the way small injuries can be precursors to larger injuries. In 1969, building upon the work of Herbert William Heinrich, Frank E. Bird undertook a study of industrial accidents, which resulted in one of the most widely cited findings in the history of industrial safety. For every reported major injury, there were 9.8 reported minor injuries and 30.2 property damage accidents.
In 2003, a ConocoPhillips study further solidified these findings. The study showed that for every major accident, there must be a hidden bottom end of the pyramid of at risk behaviors and smaller recordable accidents. At-risk behaviors are defined as any activity that is not consistent with safety programs or with training on machinery, such as bypassing safety components on machinery, eliminating safety steps in the production process and so on. The study found that for every loss workday incident, there were 10 recordable workplace incidents and for every recordable incident, ten near misses.
While these concepts adapted to current workplace issues provide the foundation for many safety programs, small incidents are often ignored. Most are not costly, do not disrupt workflow, and often are considered part of doing business. There’s a sense that major incidents “don’t happen here.” Boss gave three examples to illustrate the problem:
- A long-term employee of an excellent custom glass door manufacturer suffered a tragic accident and sustained a severe cut on his forearm, critically damaging the tendons and he was unable to return to work. This created internal stress as well as lost time and money. In hindsight, the pattern was showing up on the OSHA records. This was the eighth event in the handling department involving cuts. Yet, it took the severity of this incident to propel a conscientious employer to action.
- The number one salesperson at a lumber company was showing a client around the facility on the day of the first snowfall of the year. He slipped and fell, suffering a fracture of the skull. Not only was this a costly accident, it also meant the loss of the top salesperson for an extended period. A review of records showed that several falls had taken place in the past two or three years during the season’s first snowstorm.
- One of the most infamous examples is the Deep Water Horizon environmental disaster in April 2010, which, tragically, killed 11 workers, and started the largest marine oil spill in history. According to the independent Deepwater Horizon study group’s final report, it was not one careless mistake, but years of cutting corners and a laissez-faire approach to safety that lead to the disaster. With a systematic effort to identify and analyze the incidents leading up to the explosion, controls could have been put in a place and a disaster averted.
A pattern of frequent, minor, workplace injuries is a red flag that should alert employers to dangers ahead if no actions are taken to resolve the underlying causes. As Dustin Boss concludes, “Major injuries are rare events and many opportunities are afforded by the more frequent, less serious events to take action to prevent the major losses from occurring.”
SEVEN SECRETS
You’ll receive important information to help you avoid overcharges on your workers’ compensation.