Seven common mistakes in workers comp when hiring subcontractors
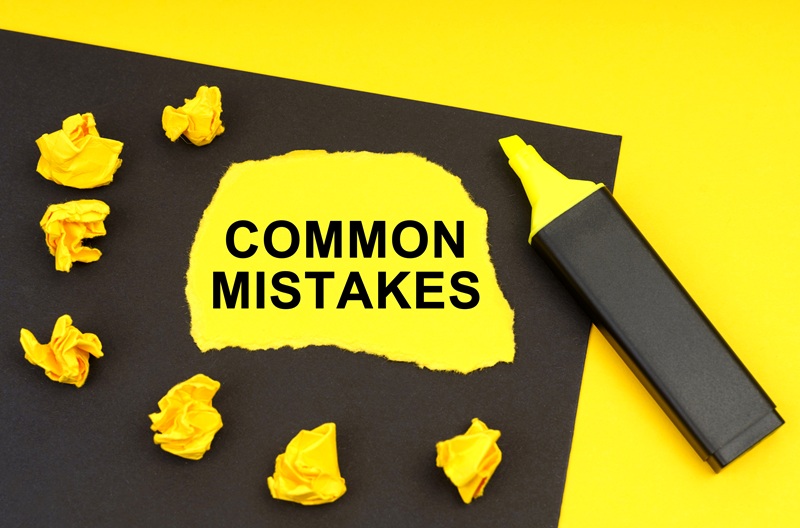
Subcontractor mistakes in workers comp can lead to significant financial and legal issues for the contractor and/or project owner. Here are tips on avoiding seven common mistakes:
- Choosing a subcontractor based on price alone
While budget constraints are significant, choosing a subcontractor solely based on the lowest bid can lead to problems. Look for a balance of cost, quality, and reliability. To win a bid, a low-cost contractor may compromise on materials, craftsmanship, insurance, or essential processes, resulting in poor-quality construction or unexpected delays.
How to avoid this mistake
- Establish a robust subcontractor qualification program that thoroughly vets subcontractors. Verify licensing, certifications, insurance, experience, expertise, reputation, management team, financial stability, hiring practices, safety records, and risk management processes.
- Insist on itemized estimates that include labor, materials, permits, insurance other expenses, and timelines. This could reveal unrealistic pricing, omitted costs, incompetence, poor quality materials, or failure to understand the project’s scope.
- Before hiring, review the subcontractor’s roster of work.
- Inadequate verification of insurance
Most contractors know that subcontractors should carry workers compensation (and employers’ liability) and general liability insurance and provide Certificates of Insurance (COIs) to prove coverage before beginning work at the site. However, simply having a COI is not sufficient. We have seen countless situations where subs are picked up as uninsured during a work comp audit, even when a certificate is on file. When this happens, the auditor will include the subcontractor’s payroll in calculating your comp premium, and you will be responsible for any medical expenses, lost wages, and other injury-related costs.
How to avoid this mistake
- Review the COI carefully and verify the details (company name, policy number, effective dates, coverage types, and limits) to ensure it is valid and covers all employees. Be sure the COI lists work comp coverage and verify the limits are adequate.
- For repeat subcontractors, get updated COIs on each new job. Don’t assume an existing certificate is valid.
- Include strict insurance requirements in contracts.
- Have a system that tracks COIs to ensure the coverage is in effect the entire length of time that the sub performed work. If the subcontractor’s policy expires before work is finished, a new COI must be obtained to prove renewal. This is a critical administrative task and the only way to avoid audit surprises and unexpected costs.
- Discuss your subcontracting practices with your insurance agent to ensure you comply with all applicable laws and to help you identify potential issues.
- Don’t require a breakdown of material and labor costs from subcontractors
While it is a best practice only to hire insured subcontractors, sometimes it’s impossible, or there is an unexpected lapse in coverage. It’s important to minimize your exposure when this occurs.
How to avoid this mistake
- Require all subcontractors to submit invoices with breakdowns of material and labor costs. This will allow the auditor to exclude materials from the additional audit charges.
- No protection if subcontractor policy is canceled
COIs are snapshots in time. They only reflect the active coverage as of the issued date and don’t guarantee coverage in the future. Many states don’t require policyholders or insurance companies to notify additional insured or affected parties when a policy is canceled, so you may not be notified.
How to avoid this mistake
- When possible, add provisions to the contracts to require notification of the insurance company’s and/or subcontractor’s intent to cancel.
- For longer projects, periodically verify the coverage by calling the insurance company or use a service that specializes in verifying the insurance status of subcontractors.
- Keep good records about what work subcontractors were hired to do and when they did This can limit exposure if coverage is canceled.
- For coverages other than workers’ compensation, it may be advisable to require your business be named as an additional insured. An additional insured status offers a layer of protection, but it’s best to consult your legal or insurance professionals to ensure the proper risk transfer mechanisms for maximum protection.
- Get confused by state laws about work comp coverage and exemptions
In many states, workers’ compensation is mandatory for businesses with one or more employees. Still, some states have a threshold for a certain number of employees before workers’ comp is required. However, just because a subcontractor doesn’t have a legal requirement to have comp, it doesn’t remove the responsibility to have it during your contract.
Also, some states allow sole proprietors, members of limited liability companies (LLCs), and corporate officers who own a certain percentage of company stock to opt out of comp. COIs may not indicate if there are exemptions or exclusions to the work comp coverage.
How to avoid this mistake
- Require all subcontractors to provide COIs regardless of state laws regarding work comp coverage.
- The laws for exemption vary by state, and contractors should handle exemptions carefully to ensure compliance with state laws and mitigate liability risks. Don’t accept the subcontractor’s position as fact – be sure you understand the applicable laws. Require subcontractors or independent contractors claiming an exemption to provide official proof. Be sure to review these with your insurance agent.
- Misclassification of subcontractor as independent contractor
Misclassifying subcontractors as independent contractors, whether willful or accidental, is a common and costly mistake. Some subcontractors may attempt to misrepresent their independent contractor status, out-of-state subcontractors may try to apply exemptions from one state to another or to claim that the other state’s coverage is sufficient, or subcontractors may hire individuals or other subcontractors who are unverified independent contractors. A 2023 study by The Century Foundation found up to 2.1 million construction workers are illegally misclassified or paid off the books.
Such misclassification exposes employers to legal penalties and increased liability. Every state has different standards, but most relate to control over the method and way the work is completed.
How to avoid this mistake
- Know the state rules governing independent contractors and the state and federal rules for joint and statutory employers.
- Clearly define the relationship and reinforce independence in the written contract; be clear about their roles, responsibilities, and the nature of the work subcontractors will perform to avoid misclassification.
- Require subcontractors to sign agreements stating they are responsible for their workers.
- Avoid direct control over the subcontractor’s workers.
- Document all subcontractor relationships(W-9s, invoices, payment records) to show a clear separation.
- Fail to vet and monitor subcontractors for safety compliance
A company’s Experience Mod is a common gauge used as a safety measure when hiring subcontractors. If it is below 1.0, it’s considered good. However, many safety experts and the NCCI have taken the position that the Mod is not a good measure of a company’s safety record, as there are many factors unrelated to safety that go into the calculation of a Mod. Using this measure can be particularly detrimental to smaller companies with strong safety records.
Even if you have experience with the subcontractor, oversight throughout the life of the project is essential to ensure compliance with safety protocols.
How to avoid this mistake
- Consider using alternative methods to the Experience Mod to gauge a subcontractor’s safety record. For example, OSHA recordable data are explicitly intended to be safety performance metrics and are calculated in a way that makes employers of any size comparable.
- Include safety requirements in all subcontracts, defining specific safety standards, training requirements, compliance expectations, and the consequences for non-compliance.
- Develop a comprehensive site-specific safety plan that includes subcontractors.
- Hold daily or weekly safety meetings to discuss potential hazards and best practices.
- Conduct routine safety inspections and audits to identify risks and ensure compliance with all safety policies. Address any issues immediately.
- Establish a system for reporting and addressing safety violations and encourage workers to report safety violations or hazards.
- Document all safety compliance efforts and track incident reports, near misses, and corrective actions.
Contractor and subcontractor relationships are complicated insurance transactions. As CWCAs we are here to help.
SEVEN SECRETS
You’ll receive important information to help you avoid overcharges on your workers’ compensation.